Cage Storage 2018
Overview
The re-design and remaking of the cage’s large storage system was taken on by 3rd year student Yesha Subotincic West. This was done in the late spring and early summer of 2018. It was being designed and built as a negotiated project with funding from the RCS.
Proposal
Problem
The cage is an essential part of any work onstage. As it is a place for keeping all the heavy and expensive gear, and the organization for the storage of this gear is crucial. The better it is stored, the better the stage will run. The cage storage, at the moment, is far from ideal. The old storage unit is made of non-durable ply and timber. The boxes are different sizes and it is awkward to re-arrange and pull gear out of it. The lifespan of this unit is limited and is in constant need of repair and re-organization.
Proposed Solution
The proposed solution is a durable metal frame with removable boxes for storage. The storage frame is made of welded 20x20 box steel and topped with birch ply. The boxes can be re-arranged in the frame as well as removed and brought onstage. The boxes have handles to pull and hold at the front as well as handle holes on the sides. These boxes are made of durable birch ply and glazed to prevent the wood from tarnishing. The frame and boxes are designed to be as versatile and “idiot proof” as possible.
Planning
The final plans were made up with cut-lists. This meant that when it came to making cuts, the lists were already prepped and ready to go. This preparation paid off greatly when working to a tight time frame.
The original plan consisted of a 16 box large unit in the cage, redone to accommodate 3 boxes and a rolling storage frame. The box size was larger than the finished product. The frame had a place for boxes of truss eggs, pins and clips as well as the turfer. The plans below show the construction drawings, rendering, and the costing.
The original design cost came to nearly £500 which was too much. The plan included storage boxes for the existing table in the cage and a rolling work surface what included shelves for large and small plastic storages boxes. This was supposed to allow large amounts of gear to be brought to and from the stage more easily, while also providing a portable secure work surface. For storage and money reasons these were cut. To reduce costs further, the entire large storage container was scaled down to the smallest size possible. This brought the total cost down to just over £300.
The final plans show the cut to the amendments listed above. With the price of birch ply shooting through the roof, the size of everything had to be scaled down too. Below are the final plans and costing.
In discussion with Malcolm, it was decided to make two extra boxes and scrap the storage for the turfer and amo-boxes.
Process
The process is broken into 2 sections. Boxes and frame, in wood and metal respectively.
Boxes
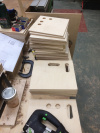


The process began with cutting all the parts of the boxes. This started with cutting enough pieces for 18 boxes, and since “in theory, theory and practice are the same but in practice they’re different,” there ended up being a bit more material available than first anticipated. The number of boxes therefore, was bumped up to 20.

The process of construction started with assembling one box to the exact specifications on the drawing. Originally an existing handle jig was used. This was the jig that was used to make handles in rolling dollies. It turned out the handles were too big. It also turned out that the original idea of pulling the boxes out of the storage frame by the front or supports in the top would not work. When the box was made up, it was decided to add a second handle to the front of the side. In this way the box can be pulled out by the front handles and lifted by the top handles. The handles were made and drilled out on each end and then jig sawed. The jig was then screwed onto the side and routed out using a router bit with the guide on top.
The back and base were pre-drilled with a countersink. The boxes then got assembled using a previously completed box as a guide to keep things square. The bottom and back were then glued and screwed, to make a right angle. The sides where glued and screwed, far easier, in correct alignment.
Once the main part of the boxes was complete, the front could be attached and routing could happen to finish the edges. The inside ¾ of the front side edges had to be routed before the fronts were attached. As well, one long edge of the front had to be routed on both sides before being attached. An important lesson I learned here was if the router base was against the wood, there was less likelihood that the ply would split. I was having a lot of trouble with this in the beginning however, I eventually discovered this and found a process that allowed me to router the majority of the edges without splitting, i.e. with the router base on the face of the piece rather than on the edge. The front was then spread with glue and nailed on with an air-brad nail gun and 40mm nails.
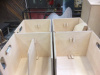
After all the edges of the boxes were rounded, all the holes were filled with what is colloquially called in the workshop - “car filler”. This is a nasty smelling, fast setting, epoxy-like filler. Once this had set, the boxes were sanded and glazed with Flints Matte Glaze. It takes approximately .5L to glaze 5 boxes.
With some of the leftover material, 4 boxes got fitted out with dividers. This was comprised of 6 small blocks of wood used to guide and hold the divider in place, and the divider itself.
Frame
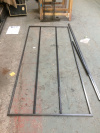



The process for the frame started with cutting the long lengths at 45 degrees. F.H. Brundle only had half of the material in stock, so it was delivered in two loads. The face frames were welded first and then connected to make the final structural unit with the angle sliders. Before welding the first face could be tacked, each piece was marked out with the positions for the cross pieces and vertical dividers. The square frame was tacked and welded, and then the horizontal dividers were tacked and then welded. Following this the vertical dividers were then put roughly into place. Using a long section of 20x20, the three pieces were clamped to it, in a line, so that they were guaranteed to be straight with respect to each other. This was lined up to the mark on the frame and then tacked and welded. The second face was tacked on top of the first one to make sure they were exactly the same. It was then removed and welded. With both faces complete the angled sliders for the boxes needed to be added in order to attach both faces together. They were tacked to the back face and then this was balanced with the angle facing downward onto the front face. Each piece was lined up and tacked on the front face. The whole frame was lifted off and the bottoms of the double angles were then welded, and then the tops were tacked. The single angles were then welded on two sides. To finish, a general sanding with an angle grinder was done to the welded edges. The whole frame was cleaned again with meths and got a through coat of shellac to prevent rusting. The front visible part of the frame was coated with matte Plastikote black spray paint.
Welding the frame square
One short end of the frame was clamped to a rip of ply screwed to the working table. This mean that one end of the frame was guaranteed to be square. The rest of the frame was laid out flat on the table and tacked on the outside edge. The frame was measured from corner to corner and adjusted until each measurement was within 2mm of each other. It was then clamped down and tacked on the inside. This kept it square until it is welded properly.
Completion
Although the whole project was completed in time, it could not be properly installed into the cage for the deadline.
Things Learned
• Turn the compressor on before using the wall saw
• It’s all in the preparation. Make the jig right, and it’ll be fine.
• Countersinks are really useful.
• Square up the sheet of ply by cutting a sliver off one end.
• When welding: make the settings in the middle of the range for the material you’re welding and then adjust as necessary.
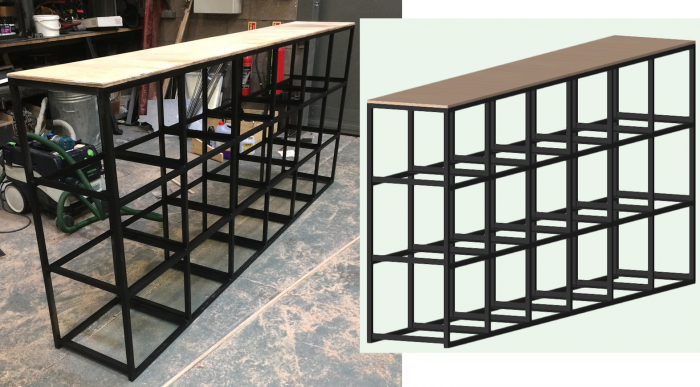
Word Count
1516