What I Meant Was...: Difference between revisions
Line 67: | Line 67: | ||
The set consisted mainly of steel deck, with a different height at the back. This was behind a white gauze, surrounded by black masking to create a frame. This was then projected onto with different images and clips for each play. | The set consisted mainly of steel deck, with a different height at the back. This was behind a white gauze, surrounded by black masking to create a frame. This was then projected onto with different images and clips for each play. | ||
[[Image:WIMW Plan.jpg| | [[Image:WIMW Plan.jpg|center|500px]] | ||
==Technical Challenges== | ==Technical Challenges== |
Revision as of 21:16, 14 June 2011
What I Meant Was... | ||||||||||||||||
---|---|---|---|---|---|---|---|---|---|---|---|---|---|---|---|---|
![]() | ||||||||||||||||
What I Meant Was...
|
What I Meant Was... is a drama piece of 8 short American plays, which is being performed at the Tron Theatre Glasgow.
Production Team
Production Manager Sandy McRobbie
Stage Manager Catherine Lewis
Deputy Stage Manager Laura Jarvis
Assistant Stage Manager James Gow and Sean Hind
Lighting Designer Ian Swinscoe
Sound Designer Jonny Reed
Production Electrician Craig Ralph
Technical Stage Manager Fiona Nisbet
Lighting Operator Fiona Findlater
Sound Operator Michael Parkin
Lighting Crew Suzie Inglis and Sophie Martin
Technical Crew Jade Beatson and John Beggan
Set
The set consisted mainly of steel deck, with a different height at the back. This was behind a white gauze, surrounded by black masking to create a frame. This was then projected onto with different images and clips for each play.
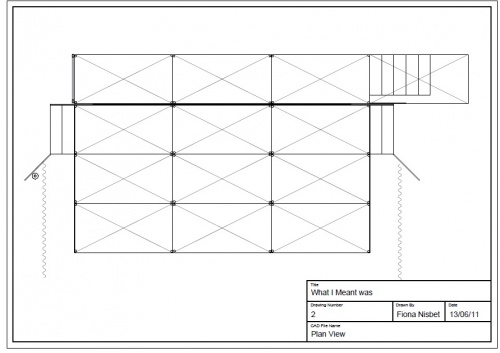
Technical Challenges
Washing Line
During 'Action' a washing line needed to be in place US, 3 metres high. The original idea was to have two pieces of scaff at 2500mm, attach a scaff foot to one end and a screw jack to the other and place one in each wing. Once they were in place they could then be tightened between the floor and the bottom of the fly floor. On SR, a clamp with an eye on it would then be attached to the top of the bar, and on the other side a cleat to keep the washing line tight. From each of these points, on both sides, black sash would be tied on and attached to a pulley. The washing line would then go through the pulley so that the actors could stand on a chair and move the washing line on stage.
This plan ended up not being right however, as the ceiling in the wings is only plaster board and not strong enough. In the SR wing there was a beam in the ceiling, so we could still use the idea on one side. For the other we ended up using a hook attached to a snap hook with some sash, which during the scene change would be connected to the washing line pulley that had a snap shackle. However, because the hook on SL was lower than the point SR it sat at an odd angle onstage and another line had to dropped from the fly floor and the snap hook attached to that as well. So during the scene change, I would pass an actor on stage the pulley, it would be taken across the stage and hook to the snap hook hanging from the fly floor.
Gauze and Frame
Originally, the designer wanted the masking around the frame to be hard masking, but this was going to be too expensive, so was changed to soft. The masking and the gauze had to be very close together for the projection, to the top border, legs, and the gauze were all put on the same bar. This gave us no play with the legs however, as they did not reach the ground when the bar was grided. This problem was solved by hanging a short piece of scaff from each end of the bar, and putting piece of rope through the scaff and tying it onto the counter weight bar, which meant that the bar would self level itself and the leg would always sit straight. For the masking on the bottom of the frame, hard masking was used, which was kept in place by screwing it to the steel deck.